Monday, September 30, 2013
3 Input Video MUX Cable
The circuit diagram shows a low-cost 3-input video MUX cable driver. In this circuit, the amplifier is loaded by the sum of RF and RG of each disabled amplifier. Resistor values have been chosen to keep the total back termination at 75 Ω while maintaining a gain of 1 at the 75-Ω load. The switching time between any two channels is approximately 32 ns when both enable pins are driven. When designing a circuit board for this cable driver, care should be taken to minimize trace lengths at the inverting input. The ground plane should also be pulled away from RF and RG on both sides of the board to minimize stray capacitance. Current consumption of the cable driver is a modest 8mA.
Sunday, September 29, 2013
Two LED Voltage Indicator
Assuming for the moment that R1 is not commented, the output of IC1.A is a square wave with almost 50% duty cycle. The voltage at the junction of R2 and C1 will be a triangular wave (again, almost) with a level determined by the difference in the two threshold voltages of the NAND Schmitt trigger gate IC1.A. IC1.B, IC1.C and IC1.D form inverting and noninverting buffers so that the outputs of IC1.C and IC1.D switch in complementary fashion. With a 50% duty cycle, the red and green LEDs will be driven on for equal periods of time so that both will light at approximately equal brightness resulting in an orange-yellow display. With R1 in circuit, the actual input voltage to IC1.
This is shown in dashed outlines in the circuit diagram. With an 8.2 V zener the dropper resistor should be around 220 ? and R1 has to be reduced to 4.7 k. The LED brightness is determined by R4. As a rule of thumb, R4 = (Vsupply – 2) / 3[k] and remember that the 4093 can only supply a few mA’s of output current. Applications of this little circuit include ‘non critical’ ones such as go/non-go battery testers, simple temperature indicators, water tank level indicators, etc.
Saturday, September 28, 2013
Courtesy Light Extender
This allows Q2 and Q3 to turn on and the courtesy lamp is activated. When the door is closed, the courtesy lamps stay illuminated and the 33µF electrolytic capacitor starts charging through the associated 1MO resistor. As the voltages rises, Q1 turns on slowly, turning off Q2 and Q3 which gradually fades out the courtesy lamp. If a lock signal from the central locking system is received, relay 1 closes and charges the capacitor instantly, so the lamp turns off immediately. Relays were used to interface to the central locking/alarm system as a safety feature, to provide isolation in case something goes wrong.
Friday, September 27, 2013
Long Delay Timer Circuit
Suitable for battery-operated devices, Fixed 35 minutes delay
This timer was designed mainly to switch off a portable radio after some time: in this way, one can fall asleep on the sand or on a hammock, resting assured that the receiver will switch off automatically after some time, saving battery costs.
Circuit operation:
R1 and C1 provide a very long time constant. When P2 is momentarily closed, C1 discharges and the near zero voltage at its positive lead is applied to the high impedance inputs of the four gates of IC1 wired in parallel. The four paralleled gate outputs of the IC go therefore to the high state and the battery voltage is available at Q1 Emitter. When P2 is released, C1 starts charging slowly through R1 and when the voltage at its positive lead has reached about half the battery voltage, the IC gate outputs fall to zero, stopping Q1.
This transistor can directly drive a portable radio receiver or different devices drawing a current up to about 250mA. Connecting a Relay across the Emitter of Q1 and negative ground, devices requiring much higher voltage and current operation can be driven through its contacts. Pushing on P2 for 1 to 5 seconds, the circuit starts and then will switch off after about 35 minutes. This time delay can be varied by changing R1 and/or C1 values. P1 will stop the timer if required.
LED D1 is optional and can be useful to signal relay operation when the load is placed far from the timer.
Circuit diagram:
Long Delay Timer Circuit Diagram
Parts:
R1_________10M 1/4W Resistor
R2_________4K7 1/4W Resistor
R3_________1K 1/4W Resistor (Optional, see Text)
C1_________220µF 25V Electrolytic capacitor
D1_________LED any type and color (Optional, see Text)
D2_________1N4148 75V 150mA Diode (Optional, see Text)
IC1_________4011 Quad 2 Input NAND Gate CMos IC (See Notes)
Q1_________BC337 45V 800mA NPN Transistor
P1,P2______SPST Pushbuttons
RL1________Relay with SPDT 2A @ 230V switch (Optional, see Text)
Coil Voltage 12V - Coil resistance 200-300 Ohm
Notes:
- A 4011 Quad 2 Input NAND Gate was used for IC1, but many other CMos gates or inverter arrays can be used in its place, e.g. 4001, 4002, 4025, 4012, 4023, 4049, 4069. With these devices, all inputs must be tied together and also all outputs, as shown in the Circuit diagram.
- The operating voltage of this circuit should lie in the 6 - 12V range.
Source: www.RedCircuits.com
Thursday, September 26, 2013
2012 Hyundai Genesis Owners Manual
maybe you will need this owner manual so we provides post about this vehicle. beware before you download please to make sure you know this pdf is not on our hosted.
readour privacy first before you download this 2012 Hyundai Genesis Owners Manual
Wednesday, September 25, 2013
Battery powered Night Lamp Circuit
Ultra-low current drawing 1.5V battery supply
This circuit is usable as a Night Lamp when a wall mains socket is not available to plug-in an ever running small neon lamp device. In order to ensure minimum battery consumption, one 1.5V cell is used, and a simple voltage doubler drives a pulsating ultra-bright LED: current drawing is less than 500µA.
An optional Photo resistor will switch-off the circuit in daylight or when room lamps illuminate, allowing further current economy.
This device will run for about 3 months continuously on an ordinary AA sized cell or for around 6 months on an alkaline type cell but, adding the Photo resistor circuitry, running time will be doubled or, very likely, triplicated.
Circuit diagram :
Battery-powered Night Lamp Circuit diagram
Parts:
R1,R2___________1M 1/4W Resistors
R3_____________47K 1/4W Resistor (optional: see Notes)
R4____________Photo resistor (any type, optional: see Notes)
C1____________100nF 63V Polyester Capacitor
C2____________220µF 25V Electrolytic Capacitor
D1______________LED Red 10mm. Ultra-bright (see Notes)
D2___________1N5819 40V 1A Schottky-barrier Diode (see Notes)
IC1____________7555 or TS555CN CMos Timer IC
B1_____________1.5V Battery (AA or AAA cell etc.)
Circuit operation:
IC1 generates a square wave at about 4Hz frequency. C2 & D2 form a voltage doubler, necessary to raise the battery voltage to a peak value able to drive the LED.
Notes:
- IC1 must be a CMos type: only these devices can safely operate at 1.5V supply or less.
- If you are not needing Photo resistor operation, omit R3 & R4 and connect pin 4 of IC1 to positive supply.
- Ordinary LEDs can be used, but light intensity will be poor.
- An ordinary 1N4148 type diode can be used instead of the 1N5819 Schottky-barrier type diode, but LED intensity will be reduced due to the higher voltage drop.
- Any Schottky-barrier type diode can be used in place of the 1N5819, e.g. the BAT46, rated @ 100V 150mA.
Source : www.redcircuits.com
Tuesday, September 24, 2013
Processor Fan Control Circuit
Fans in PCs can be objectionably loud. In many cases, the amount of noise produced by the fan can be considerably reduced by lowering its speed. Although this will decrease the amount of cooling, this need not be a problem as long as you don’t go overboard with slowing down the fan. Particularly with older-model processors, which consume quite a bit less power than the latest models, this trick can be used without any problems. This circuit is anyhow intended to be used with relatively old PCs, since more recent models generally have a fan control circuit already integrated into the motherboard. These controllers ensure that the amount of cooling is increased if the processor becomes too warm and decreased if the processor temperature is relatively low.
Circuit diagram:
Processor Fan Control Circuit Diagram:
The circuit described here consists of only a handful of components, which you will probably already have in a drawer some-where. Transistors T1 and T2 are driven into conduction by the base current flowing to the fan via P1 and D1. There will always be a current flowing through R1, and it will be approximately 120 times as large as the current through R2. R3 has been added to prevent the base current of T2 from becoming too large when P2 is set to its minimum resistance. D1 ensures that even at this extreme setting, the voltage on the base-emitter junction of T3 will still be large enough to allow it to conduct.
Monday, September 23, 2013
Comparator Based Crystal Oscillator

Sunday, September 22, 2013
Portable 9v Headphone Amplifier
Circuit Diagram:

Parts:
P1 = 22K
R1 = 18K
R2 = 68K
R3 = 68K
R4 = 68K
R5 = 18K
R6 = 68K
C1 = 4.7uF-25v
C2 = 4.7uF-25v
C3 = 22pF
C4 = 220uF-25v
C5 = 220uF-25v
C6 = 4.7uF-25v
C7 = 22pF
C8 = 220uF-25v
J1 = 3.5mm Stereo Jack
B1 = 9V Alkaline Battery
IC1 = NE5532-34
SW1 = SPST Toggle Switch
Sensitivity:
200mV RMS for 15.6mW RMS output
350mV RMS for 50mW RMS output
Maximum undistorted output: 3.6V Peak-to-peak
Frequency response: flat from 40Hz to 20KHz; -2.3dB @ 20Hz
Total harmonic distortion @ 1KHz: <0.025% at all power outputs up to 50mW RMS
Total harmonic distortion @10KHz: <0.02% at all power outputs up to 50mW RMS
Total current drawing @ 9V supply (both channels driven):
Standing current: 8.5mA
Mean current drawing @ 15mW RMS per channel: 12mA
Mean current drawing @ 35mW RMS per channel: 17mA
Saturday, September 21, 2013
Fuse Box BMW 325i 1992 Convertible Power Distribution Diagram
Fuse Box BMW 325i 1992 Convertible Power Distribution Diagram
Fuse Panel Layout Diagram Parts: Service Interval Indicator, Tachometer/Fuel Economy Gauges, Gauges/Indicators;, Brake Warning System, Back Up Lights, On Board Computer, Start, Injection Electronics, Active Check Contro, Cruise Control, Injection Electronics, Radio/Antenna, Speedometer/Indicators, On Board Compute, Front Park/Tail, Horn, Rear Defogge, Injection Electronics, Ignition Key Warning/Seatbelt Warning, Auxiliary Fan, Auto Chraging Flashlight, Ignition Key Warning/Seatbelt WarninActive Check Control, Lights, Interior Lights , Central Locking, Radio/Antenna, On Board Computer, Cigar Lighter, Radio/Antenna, Heated/Air Conditioning, Active Check Control, Front Side Marker, Headlights, High Beam Indicator, Headlight, Auxiliary Fan, Lights, Turn/Hazard Warning, Wiper/Washer, Stop Lights, Active Check Control, Antilock Braking System;, Cruise Control, Map Reading Light, Headlights, Heated Seats, Power Windows, Auxiliary Fan, Auxiliary Fan, Interior Light, Power Mirrors, Injection Electronics, Interior Lights, Radio/Antenna, Trunk Light, Active Check Control, Service Interval Indicator, On Board Computer, Tachometer/Fuel Economy Gauge, Electro Mechanical Convertible Top.
Friday, September 20, 2013
1995 Ford Ranger Wiring Diagram
![]() |
1995 Ford Ranger Wiring Diagram |
Thursday, September 12, 2013
Testing A FT245RL Chip with Software

Wednesday, September 11, 2013
KLR250 Chain Adjustment

Items Needed:
-Ft/lb torque wrench
-New cotter pin
-Basic hand tools
According to the Kawasaki KLR250 owners manual the correct way to check for proper chain slack begins with placing the bike on its side stand without a driver/passenger on the bike. Because the chain can wear unevenly you should try rotating the rear wheel (WARNING: Watch your fingers by the chain!) until you come to the part where the chain slack is tightest. Then to check for proper slack locate the swingarm guard bolt and directly under it pull the chain up toward the swingarm. The space between the chain and the swingarm should be between 0-5mm or 0-0.2" Check the diagram above for more clarity.

Once youve gotten the chain adjusted correctly all that is left to finish up this project is to tighten the axle nut to 69 ft/lbs with a torque wrench and insert a new cotter pin. Before installing the new cotter pin its best to check the chain slack one last time and youre good to go! FYI: Kawasaki recommends checking chain slack every 600 miles.
Note: Eagle eye visitors have pointed out that my adjusters are on upside down. This is the way they were when I purchased the bike. When checking my rear bearings I decided to change them back to the stock setup and found that it was much harder to keep the adjusters in place while tightening the axle nut so I changed them back to this configuration. I can only assume that is why the previous owner set them this way. It works for me so...
Tuesday, September 10, 2013
12V to 220V 100W Transistor Inverter Circuit Diagram
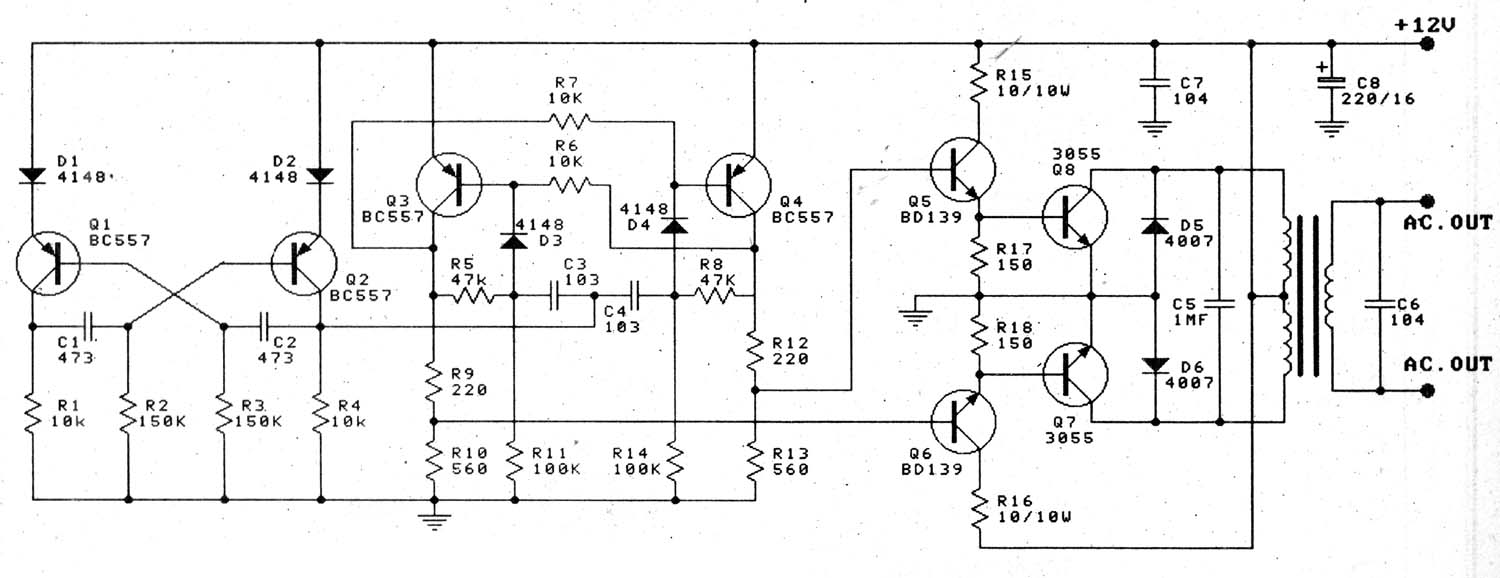
Wednesday, September 4, 2013
Radio Controlled Motor Using AF2310
Both circuits receiver and transmitter are based on the AF2310 integrated circuit .For remote control contacts you can use some push buttons or a mini-joystick .Commands are controlled by different sets of electrical contacts that are used to encode a sequence of electrical pulses; the number of pulses depends on which command is being sent.
An electrical circuit that is tuned to a frequency of 27.9 MHz creates a signal that is sent to the antenna when the pulses are active. The antenna converts the electrical energy into radio energy, creating a stream of radio energy bursts, which travel through the air and are picked up by and understood by the radio receiver in the car. The car antenna collects radio energy and transform it back into electrical energy.If the car is turned on then the radio receiver in the car is continuously monitoring the electrical energy from its antenna.
The receiver is a filter which is tuned to amplify any energy around 27.9 MHz and block energy the antenna picks up outside this region. If the Remote Control Transmitter is sending commands then its radio signal will be picked up by the receiver and converted back into the original pulse sequence. Decoding circuitry then determines which commands were sent by measuring the number of received pulses in the sequence. Signals are then sent to the motors to execute the commands.
When operated with strong batteries and in an open area the range will be at least 40 ft. Obstacles will degrade the radio signal’s ability to travel through air and reduce operating range, but will never block it completely. In the car, weak batteries will reduce power to the Motor and degrade the receiver’s ability to filter, amplify, and decode commands from the Transmitter.
When a command is received to turn left or right, a voltage is applied to the Steering Motor Since the Front Wheels are connected to the Steering Bar, the car will turn. To the turn the other direction, the voltage to the motor is reversed.The Driving Motor works the same as the Steering Motor. When a command is received to go forwards a voltage is applied to the Driving Motor; this voltage is reversed to go backwards.
Tuesday, September 3, 2013
Stereo Balance Indicator
Monday, September 2, 2013
Digital Clock Using with PIC16C54
Digital clock Circuit diagram
The common cathode for each display is turned on with transistors connected to the four I/O lines of PORTA . A low output turns on the PNP transistor for the selected display. The PORTB pins activate the LED segments.
The PORTB pins activate the LED segments. The switches are also connected to PORTB I/O pins.
When no buttons are pressed, the circuit will display the current time, starting at 12:00 on reset.
Pressing SW1 will cause seconds to be displayed. The time is set by pressing SW2 to advance minutes, and SW3 to advance hours . The displays used were common cathode and turned on with transistors to avoid trying to sink too much current into the PIC16C5X. 100 W resistors were used in series with the segments to obtain the desired brightness. Different values may be required if different displays are used.
All of the same display segments are linked together (A-A-A-A, B-B-B-B, etc.) and are individually selected by turning on only the desired display.
This simple digital clock project based on the PIC16C54 microcontroller must be powered from a simple 5 volt DC power supply circuit .
This digital clock project based on the PIC16C54 microcontroller ( circuit and software ) was designed by Dan Matthews Microchip Technology Inc . Download Source Code
Sunday, September 1, 2013
PBL3717A Motor Stepper Driver
PBL3717A Motor Stepper Driver Circuit Diagram
When both of these inputs are high the device is disabled. A separate logic input controls the direction of current flow. A monostable, programmed by an external RC network, sets the current decay time. The output current for this project is up to 1A from 10 up to 46 volt motor supply . The logic inputs I0 and I1 set at three different levels the amplitude of the current flowing in the motor winding .
A high level on the "PHASE" logic input sets the direction of that current from output A to output B and a low level from output B to output A. It is recommended that unused inputs are tied to pin 6 (Vss) or pin 4 (GND) as appropriate to avoid noise problem. The current levels can be varied continuously by changing the reference voltage on pin 11. In this bipolar stepper motor driver project , the Vss is the logic power and must be around 5 volt and VS is the motor power and must be between 10 and 46 volts .